人工智能(AI)正被各行各业采用,以利用数据的力量并利用它做出更明智的决策。本文将介绍如何识别人工智能在机器视觉应用中的机会。AI系统的业务需求管理期望AI方法具有特定的用例。毕竟,它不是万能的解决方案,不能解决所有问题。有些应用程序更适合传统的计算机视觉,有些可能需要两者,有些可能只需要人工智能。人工智能系统在成本和前期所需资源方面都很昂贵。开源工具需要大量的开发时间,而外部工具通常很昂贵。此外,通常需要GPU才能在系统上实现足够的性能。许多制造商往往没有GPU或同等的处理能力。因此,重要的是要确定哪些应用程序非常适合具有强烈业务需求的AI。视觉系统设置的重要性在进入AI之前,建议先打好视觉系统设置的基础。然而,这对于AI来说并不重要,它通常可以处理比传统系统更糟糕的情况。所有常用的机器视觉系统规则都适用于此——良好的照明、相机分辨率、焦距等。如果这些因素中的任何一个不符合标准,那么在深入研究AI之前回过头来解决这些问题是值得的。确保强大的视觉系统设置以获得最佳结果。参考人类绩效人工智能系统在人类绩效很强的地方最为成功。系统设置完成后,操作员可以轻松地通过眼睛识别/分类图像,从而确定它是否适合AI。但是,如果人类的表现达不到要求,那么AI模型很可能表现不佳。将人类表现作为AI模型可以实现的目标的参考点,如果操作员在识别图像时只有70%正确,那么AI不太可能表现得比这更好。因此,如果人类的表现对于应用程序而言不够好,则应首先解决该表现并将其提高到可接受的水平。一旦操作员达到了预期的性能,就可以考虑人工智能。时间和资源收集图像和训练模型需要付出相当大的努力。通常,收集高质量图像是最困难的部分,因为许多制造商的缺陷数非常低。如果数据缺失,则很难训练有缺陷零件的模型。训练工具很有用,它提供了需要更少样本进行训练的预训练模型。训练是一个迭代过程,跨越多个步骤以找到模型执行的理想参数。优化模型通常需要时间和实验。此外,如果新数据进入现场,则需要重新训练和部署模型。人工智能应用实例:人工智能在机器视觉中的一个应用实例是用于总装检测,另一个是印刷电路板或印刷电路板检测。最终装配检验:背景零件/产品或装配的最终检验通常由操作员或传统机器视觉系统或两者共同完成。Teledyne相机将在此处作为示例产品突出显示。最终检查可能会检查弯曲的引脚、表面划痕、连接器的正确放置、贴纸的对齐、文本的正确打印、机构之间的距离等等。基本上,需要找到构建过程中发生的任何异常。但是这样一来,需要快速查找的标准列表就变得很长了。传统的基于规则的系统难以处理所有边缘情况,而且培训新的操作员也很困难。为什么是人工智能?通常有太多的规则来确定什么是“通过”。这使得传统的机器视觉系统难以获得良好的性能。另一种选择是,对于很多公司来说,人工检查很费时间,而且对于新的操作人员来说,一些模棱两可的判断是很难做出的。传统的基于规则的系统往往能力不足,制造商需要依靠运营商的判断来提供帮助。可能存在不同的照明条件,以及缺陷位置、形状和纹理的高度变化。通常,只需要简单的“好/坏”定性输出。然而,如果需要,这也可以与传统的基于规则的算法相结合。好处有了AI,设置就容易多了。在收集了大量图像来训练模型后,让系统运行通常比基于规则的系统的开发工作要少得多,尤其是使用AI工具时。使用适当的系统,通常使用GPU,检查速度要快得多,大约为毫秒。在提供良好数据时,人工智能系统的表现也应该比人类更可靠,并且是标准化检查程序的好方法。该算法通常根据多个操作员提供的数据进行训练,以减少人为错误。这有助于减轻单个操作员可能遇到的任何人为偏见或疲劳。在此示例中,人工智能可以帮助制造商减少开箱即用的故障并提高检查质量和吞吐量。PCB检查:背景PCB制造商需要检查他们的电路板是否有任何缺陷。可能是焊点不良、短路或其他异常情况。通常会使用AOI(自动光学检测)机器。然而,由于缺陷变化太多,很难处理所有边缘情况。并且基于规则的系统性能不够准确,制造商会要求操作人员人工检查,既费时又费钱。为什么是人工智能?传统的AOI系统难以识别缺陷。它要么超调要么表现不佳,导致有缺陷的PCB通过或良好的PCB失败。与其他情况类似,判断一块“好板”的规则太多了。根据应用的不同,AI可用于对尺寸和形状差异很大的缺陷进行分类,例如短路、开路、错误组件、焊接缺陷等。好处借助人工智能,制造商可以提高检查的准确性和质量。这有助于减少通过检查的有缺陷PCB的数量。同时,它节省了任何人工辅助检查的时间和人力成本,并通过自动化操作员需要更长时间才能完成的任务来提高吞吐量。
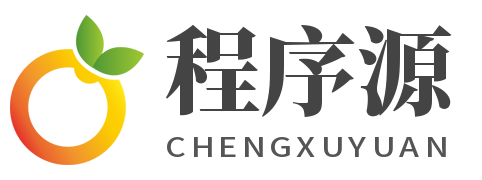