难以检测的机器故障是最昂贵的,这就是为什么经验丰富的维修技术人员如此抢手的原因。如今,许多制造公司都在寻找自动化和降低维护成本的解决方案。随着自动化和数字化的深入,新设备依赖传统的振动诊断方法可能为时已晚,因为大多数维护人员可能无法提前检测到故障。德勤的一份报告指出,在工业4.0的背景下,预测性维护的好处取决于行业或其应用的具体过程。德勤当时的分析得出的结论是,材料成本平均节省了5%到10%;设备正常运行时间增加10-20%;总体维护成本降低5-10%;维护计划时间甚至减少了20-50%!例如NeuronSoundware等公司开发用于预测性维护的AI技术。缺乏合格的维护工人踏上数字化之旅的公司通常需要面对市场上缺乏熟练劳动力的现实。通常是机械维修工,定期巡视所有机器,通过听机器的声音来诊断它们的状况。一些公司现在正在寻找新的修复技术来替代它们。未及早识别的故障意味着更换整个设备或其中的部件。整个维修时间还包括等待备件的时间,因为存放替换设备而不是存货可能会很昂贵。这将代表长达数十小时的停机时间。损失可达数万甚至数百万。如果维护技术在机器的机械知识之外配备人工智能,那么对机器进行实时监控是一种趋势。它将此知识本身应用于机器的当前状态。它还能够识别机器上当前发生的异常行为。在此基础上发出相应的告警和精准的维修指导。例如,如今电梯、自动扶梯和移动设备等机械制造商都在使用这项技术。人工智能可以在生产的各个阶段提供帮助当然,预测性维护技术具有更广泛的应用。由于AI的学习能力,它们可以变得多才多艺。例如,该技术可以帮助进行质量测试。识别产品中不可见和随机出现的缺陷部分。另一个应用领域是生产过程的监控。使用岩石破碎机的例子来形象化这一点。传送带将不同尺寸的石头输送到研磨机,研磨机生产给定粒径的砾石。以前,制造商会按预定时间运行破碎机。确保即使存在最大的岩石碎片也能发生足够的破碎。使用人工智能“聆听”砾石的大小。他可以在正确的位置停止破碎过程。这不仅意味着减少破碎设备的磨损,而且更重要的是,可以节省时间并增加每班次的砾石输送量。这给生产者带来了巨大的经济效益。拥有大型同质设备资产的公司受益更多。在实施预测性维护技术时,公司的规模并不重要。最常见的决策标准是已部署解决方案的可扩展性。在拥有大量类似机制的公司中,可以快速收集代表个别问题的样本。神经网络从中学习。然后它可以同时处理任意数量的机器。机器越多,神经网络学习和检测的效率就越高。预测性维护的未来:可用性和自适应状态监测技术通常是为大型工厂设计的,而不是为只有几台机床的车间设计的。然而,随着硬件、数据传输和处理变得更便宜,该技术正逐渐得到更广泛的应用。因此,即使是自制果酱制造商也会很快获得信心,相信他的机器将生产出足够的产品,以便在不损害他的声誉的情况下按时将订单交付给客户。在未来,预测性维护将是必要的。不仅是工业制造,还有我们日常生活中的那些设备(比如汽车,各种家用电器等)。通过安装人工智能驱动的自动检测设备,我们将及时了解即将发生的故障并能够及时解决问题,而不是在设备出现故障时致电服务提供商并焦急地等待上门维修服务。
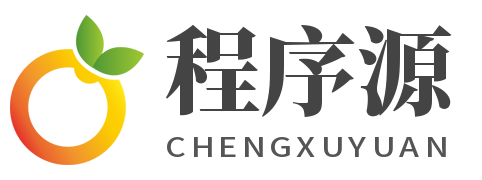